Innovation Let Loose: Advancing Casting Aluminum Illinois
Innovation Let Loose: Advancing Casting Aluminum Illinois
Blog Article
Technology in Aluminum Spreading: Cutting-Edge Techniques for Modern Developers
What absolutely sets these technologies apart are the lasting aluminum alloys being created and the high-pressure die casting techniques that are revolutionizing the sector. Join us as we explore the leading edge of aluminum casting innovation, where technology meets imagination to redefine what is possible in the globe of metal spreading.
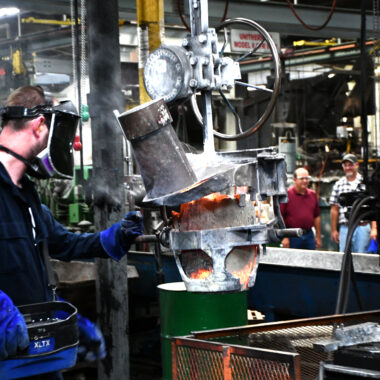
Advanced 3D Printing Methods
Using sophisticated additive manufacturing procedures, progressed 3D printing strategies have transformed the production of intricate and tailored aluminum components. By employing high-precision printers that can collaborate with aluminum powders or filaments, producers can develop complicated geometries and styles that were formerly unattainable with traditional manufacturing techniques.
One of the vital advantages of innovative 3D printing in light weight aluminum element manufacturing is the ability to attain lightweight yet resilient frameworks. This is specifically useful in industries such as aerospace and vehicle, where weight decrease is vital for boosting gas performance and general performance. In addition, the modification choices offered by 3D printing permit the manufacturing of one-of-a-kind and tailored components that meet particular needs, bring about enhanced capability and performance.
Additionally, the effectiveness of the 3D printing procedure lessens product waste and reduces the overall production time, making it a cost-effective service for producing aluminum elements. As technology remains to advancement, the abilities of 3D printing in aluminum production are expected to broaden, offering also greater opportunities for innovation in numerous industries.
Computer-Aided Style Advancements
With the improvements in sophisticated 3D printing techniques for aluminum elements, the integration of Computer-Aided Layout (CAD) software application has ended up being progressively critical in driving development and effectiveness in the production procedure. CAD developments have actually transformed the method designers and engineers develop aluminum spreading mold and mildews by using accurate digital modeling abilities. These software application tools enable for the development of complex designs and simulations that optimize the casting procedure, causing higher high quality elements.
One of the vital benefits of CAD in aluminum casting is the capacity to find potential concerns early in the style phase, reducing pricey mistakes and rework during production. By imitating the casting procedure basically, designers can analyze variables such as cooling down prices, product circulation, and structural stability prior to a physical mold is developed. This aggressive strategy not only saves time and sources however likewise ensures that the last aluminum components satisfy the desired requirements.
Furthermore, CAD software program allows fast versions and modifications to styles, assisting in rapid prototyping and modification to meet certain demands. By leveraging CAD innovations in aluminum spreading, producers can improve their procedures, enhance item quality, and remain at the forefront of advancement in the industry.
High-Pressure Pass Away Casting Methods
High-pressure die spreading methods are commonly recognized for their effectiveness and accuracy in creating complex light weight aluminum parts. By using high pressure to require liquified aluminum into complex molds at fast rates, this method enables the creation of in-depth and dimensionally accurate parts. Among the vital benefits of high-pressure die casting is its ability to generate get rid of thin walls and fine details, making it excellent for applications where light-weight yet strong elements are necessary.
The process begins with the prep work of the die, which is commonly made from set tool steel and contains 2 halves that create the preferred component form. The liquified aluminum is after that infused right into the die tooth cavity under high stress, making sure that the material fills up all the elaborate attributes of the mold. When the light weight aluminum strengthens, the die opens up, exposing the completed part prepared for any necessary post-processing.
High-pressure die casting is generally utilized in numerous sectors, including auto, aerospace, and electronics, where high-volume production of intricate light weight aluminum parts is required. casting aluminum illinois. Its capability to deliver limited resistances, excellent surface coatings, and affordable manufacturing makes it a recommended selection for modern-day creators aiming to innovate in aluminum casting strategies
Sustainable Aluminum Alloys Development
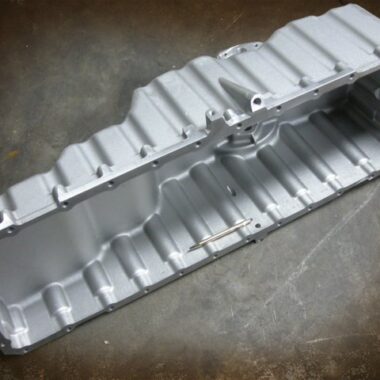
One method to lasting light weight aluminum alloy development includes incorporating recycled aluminum web content right into the alloy structure. By using recycled light weight aluminum, producers can reduce energy consumption and greenhouse gas exhausts connected with key light weight aluminum production. In addition, recycling aluminum helps draw away waste from landfills, adding to an extra circular economy.
Furthermore, scientists are exploring brand-new alloying aspects and handling strategies to enhance the sustainability of aluminum alloys. By optimizing alloy compositions and making processes, it is feasible to enhance the recyclability, toughness, and total ecological efficiency of aluminum items.

Automation and Robotics Integration
In the realm of lasting aluminum alloys development, the assimilation of automation and robotics is revolutionizing manufacturing processes, paving the way for raised effectiveness and precision in production. Automation and robotics are simplifying conventional casting techniques, supplying various benefits to designers in the light weight aluminum sector. By incorporating automation right into the casting process, repetitive tasks that were once labor-intensive can currently be effectively managed by robot systems, lowering the threat of human error and enhancing total performance.
Automated systems can function all the time, guaranteeing a constant manufacturing cycle that minimizes downtime and takes full advantage of result. Robotics integration enables complicated molds and complex layouts to be produced with unparalleled precision, meeting the demands of contemporary creators for top notch aluminum parts. The usage of automation in casting operations advertises a much safer working environment by lessening the direct exposure of workers to hazardous problems.
Verdict
Advanced 3D printing methods, computer-aided style advancements, high-pressure die spreading approaches, sustainable light weight aluminum alloys development, and automation and robotics integration have all contributed to the modernization of the casting procedure. The future of aluminum spreading is intense with continual innovation and technological improvements.
What genuinely sets these technologies apart are the sustainable aluminum alloys being developed and the high-pressure die spreading methods that are reinventing the industry. Join us as we explore the forefront of light weight aluminum casting technology, where innovation fulfills creative thinking to redefine what is feasible in the world of metal spreading.
One approach to lasting aluminum alloy growth includes integrating recycled light weight aluminum content into the alloy composition - casting aluminum illinois. By using recycled light useful link weight aluminum, producers can lower energy intake and greenhouse gas emissions connected with primary aluminum manufacturing. Advanced 3D printing methods, computer-aided design advancements, high-pressure die spreading techniques, lasting aluminum alloys advancement, and automation and robotics assimilation have all contributed to the modernization of the spreading process
Report this page